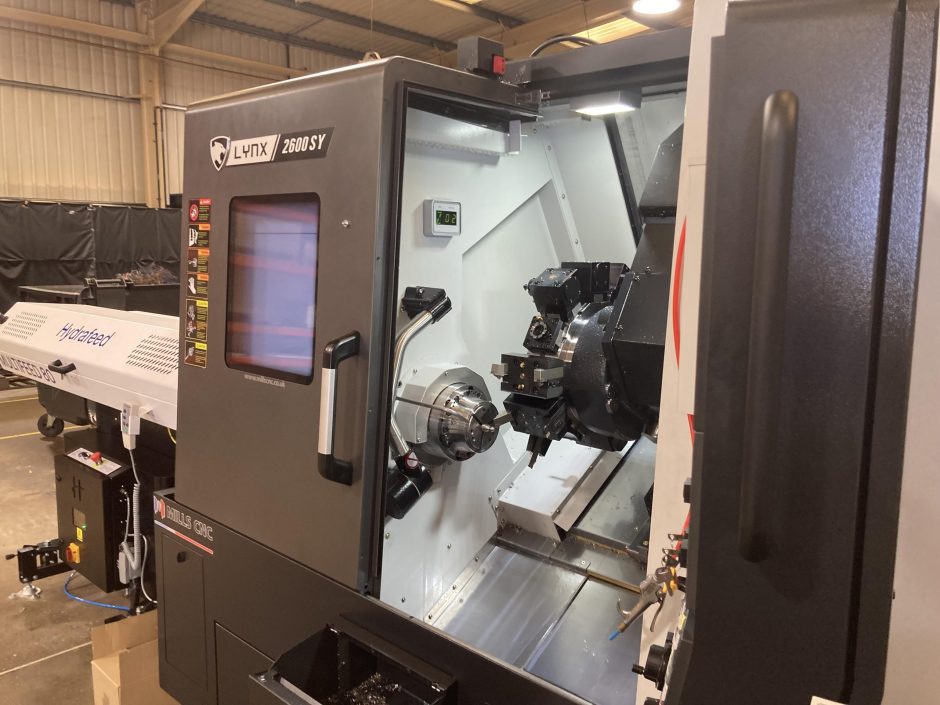
Leading precision conveyor system component manufacturer, Arnott Handling Equipment, invests in a new, multi-tasking lathe and a high-performance bar feeder from Mills CNC to help automate its small part processing operations and, by doing so, improve its productivity and process efficiencies, and maintain its competitive edge.
The latest investment underscores the company’s commitment to continuous improvement and its future business growth strategy moving forwards, where the emphasis will be on replacing older, manual equipment and labour intensive processes with sophisticated, multi-tasking technologies and automated production.
Mills CNC, the exclusive distributor of DN Solutions’ and Zayer machine tools in the UK and Ireland, has recently supplied Arnott Handling Equipment Ltd., part of the Arnott Group, and a leading UK manufacturer and supplier of components to the Conveyor and Materials Handling sectors, with a new multi-tasking lathe.
The machine, a Fanuc-controlled DN Solutions’ 10” chuck/81mm bar diameter Y-axis, sub-spindle Lynx 2600SY lathe, was installed at Arnott Handling’s 10,000sq. ft. facility in Brixworth, Northants, in June 2024 and, as part of the investment package, was also supplied with a Hydrafeed (MultiFeed 80) bar feeder to facilitate automated and unattended production.
Since being installed the Lynx 2600SY has been working flat out machining a diverse range of high-precision, engineered components and accessories for the company’s growing number of (mainly) UK-based conveyor and handling system customers.
Conveyor business
“Our customers provide a myriad of conveyor system solutions to a multitude of end-users in the retail and e-fulfilment, warehouse and distribution, food, beverage, cosmetics, packaging, pharmaceutical and logistics industries and sectors, to name but a few.
“Despite such diversity, all our customers rely on our competitively-priced, readily-available and high-quality, performance-critical components, that include gravity rollers, conveyor drums, adjustable feet etc., as well as a whole range of accessories, to build their different conveyor systems.”
Oliver Rippin Operations Director at Arnott Handling
This is big business for Arnott Handling, and, on average, the company will take and fulfil up to 500 orders for supplying its machined conveyor components to these customers, year-on-year.
One of Arnott Handling’s main customers is sister company, Arnott Conveyors Ltd., a leading design and manufacturer of bespoke conveyor systems and innovative turnkey solutions for a growing number of customers that span a wide-range of industries and sectors.
Located adjacent to one another, Arnott Conveyors operates from a separate 4000sq. ft. facility where it designs, builds, tests and proves-out up to 10 highly-customised conveyor systems for customers, prior to their on-site installation.
All machined components for these systems are supplied to order by Arnott Handling.
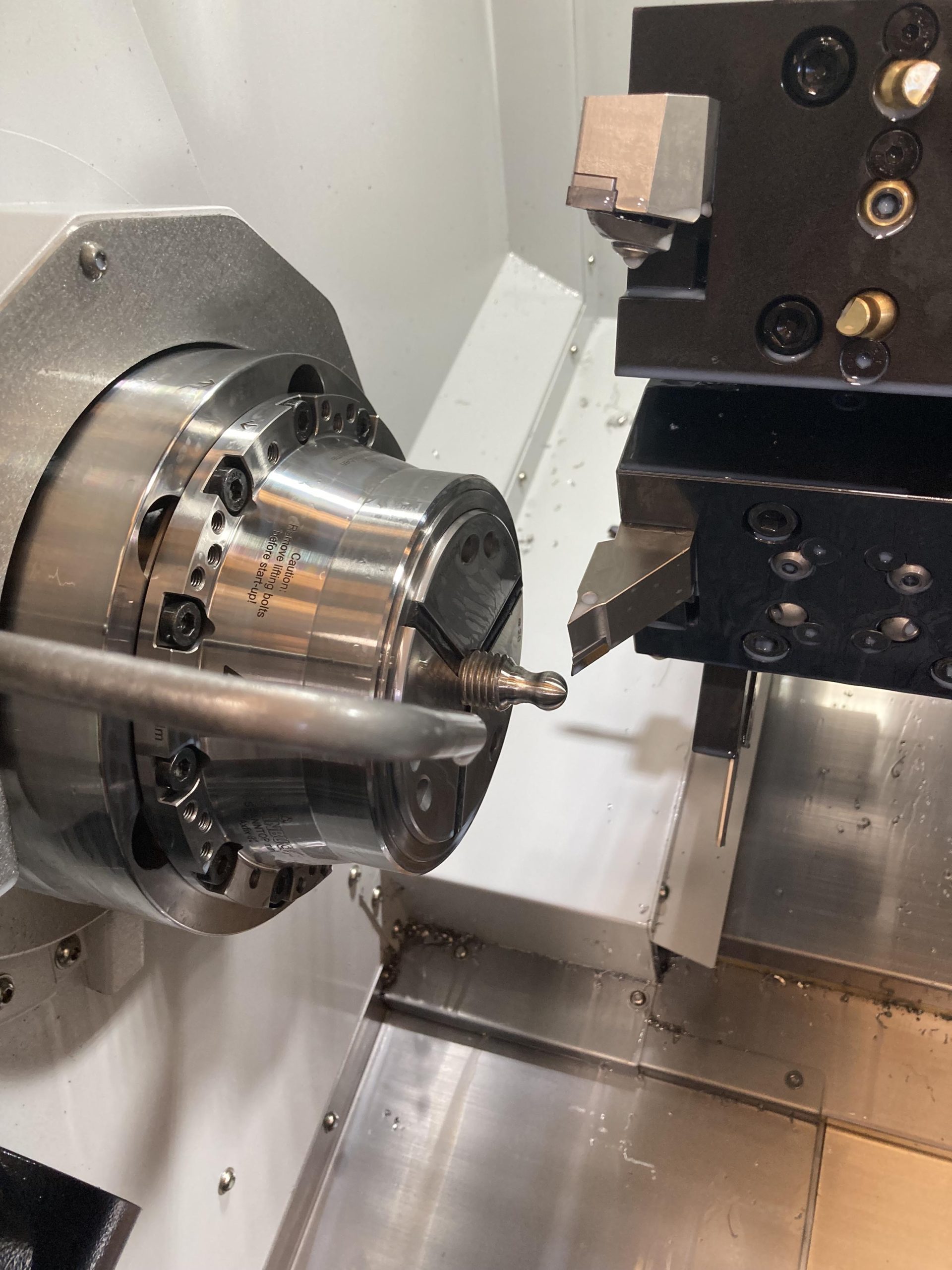
Precision subcontract business
Although relatively small by comparison in terms of annual turnover generated, the company also provides a precision subcontract machining service to other (non-conveyor) customers looking to take advantage of Arnott Handling’s extensive in-house machining capacity and capabilities, its speed of response and its specialist applications know-how.
Sustainable business growth
“Over the last 4 years sales for both our handling and conveyor businesses have been on an upward trajectory.
“As a consequence, we have invested in our people, our plant and equipment, and our processes and systems to meet the increase in demand and achieve sustainable business growth.”
Nick Howells, Commercial Director at Arnott Handling
Both companies have been successful, over this period, in capitalising on organic growth opportunities as well as winning ‘new’ business, and this has resulted in them investing in new technologies and streamlining their existing manufacturing and machining processes, where possible, to ensure that there is some ‘slack’ in the system to help them respond to new demand.
Lynx 2600SY: the Investment decision
As part of its company-wide continuous improvement programme, Arnott Handling regularly benchmarks and reviews its performance against KPIs. The monitoring and evaluation process helps identify issues and potential ‘weaknesses’ in its production processes that, if left unchecked, could affect future performance and profitability.
At the beginning of 2024, the company’s existing machining capacity and capabilities were under pressure owing to it winning a new business contract to supply a large volume of drums to a conveyor customer.
Whilst clearly being welcomed, it was apparent that this increase in demand (and Arnott Handling’s ability to meet it) would effectively ‘swallow-up’ a significant percentage of the company’s existing in-house CNC machining capacity.
“The new drum contract brought machining capacity issues to the fore – specifically relating the machining of our adjustable feet products.
“In the past, these feet, comprising two separately machined parts (i.e., a base and a threaded stem) required three different machining operations using two CNC machines (lathe and machining centre) to complete each component.
“The existing process was also labour intensive and required a machine shop member of staff to be on hand continuously to perform part loading and unloading operations.
“Because the new drum contract would significantly eat into our existing machining capacity and could cause production bottlenecks, we decided to streamline this process by investing in a new multi-axis lathe, with Y-axis and sub-spindle capabilities, to machine both the base and stem components of our adjustable feet.”
Oliver Rippin Operations Director at Arnott Handling
Having previously purchased a DN Solutions’ Puma GT 2600LM box guideway lathe from Mills CNC back in 2021, the company was familiar with DN Solutions’ turning technology, and the applications and after-sales service and support provided by Mills CNC.
Unsurprisingly Arnott Handling approached Mills to discuss its new machining requirements.
“We were introduced to the Lynx 2600SY by Mills’ sales staff and liked what we saw.
“It was immediately apparent that the machine’s sub-spindle, driven tooling and Y-axis capabilities would enable us to machine our adjustable feet components in one set-up, removing the need to transfer parts between different machines.”
Oliver Rippin Operations Director at Arnott Handling
Furthermore, the integration of a high-performance bar feeder, delivered to Arnott Handling as part of the investment package, would enable the company to create a flexible, high-productivity automated manufacturing cell and, as a consequence, capitalise on unattended production.
Adjustable feet
Arnott Handling’s adjustable feet are machined from solid billet and threaded bar in small to medium volumes – typically 200 – 300-off.
The materials machined vary, according to the end application and include – mild steels, stainless steel 314 and 316, aluminium, titanium, end engineering plastics (i.e., Nylon, Acetal etc.).
Machine cycle times are short (typically a couple of minutes for both the base and stem components), and part tolerances and surface finish requirements can be tight.
The company machines its adjustable feet for stock, enabling it to respond quickly to its conveyor customers’ demands. Adjustable feet are available in different sizes (base diameters and shapes, thread lengths etc.), and with different load bearing capabilities.
They can be designed for specific applications (i.e. with metal, plastic or anti-bacterial bases) and can also be supplied with zinc-plated bases that prevent corrosion.
(Interestingly, not all requests for Arnott Handling’s adjustable feet are from ‘conveyor’ customers and, only recently, the company has fulfilled two orders to supply both a wheelchair ramp and a hot tub manufacturer with these products).
Since being installed over 2 months ago, the Lynx 2600SY automated manufacturing cell hasn’t missed a beat and is meeting its quality and productivity targets, as intended.
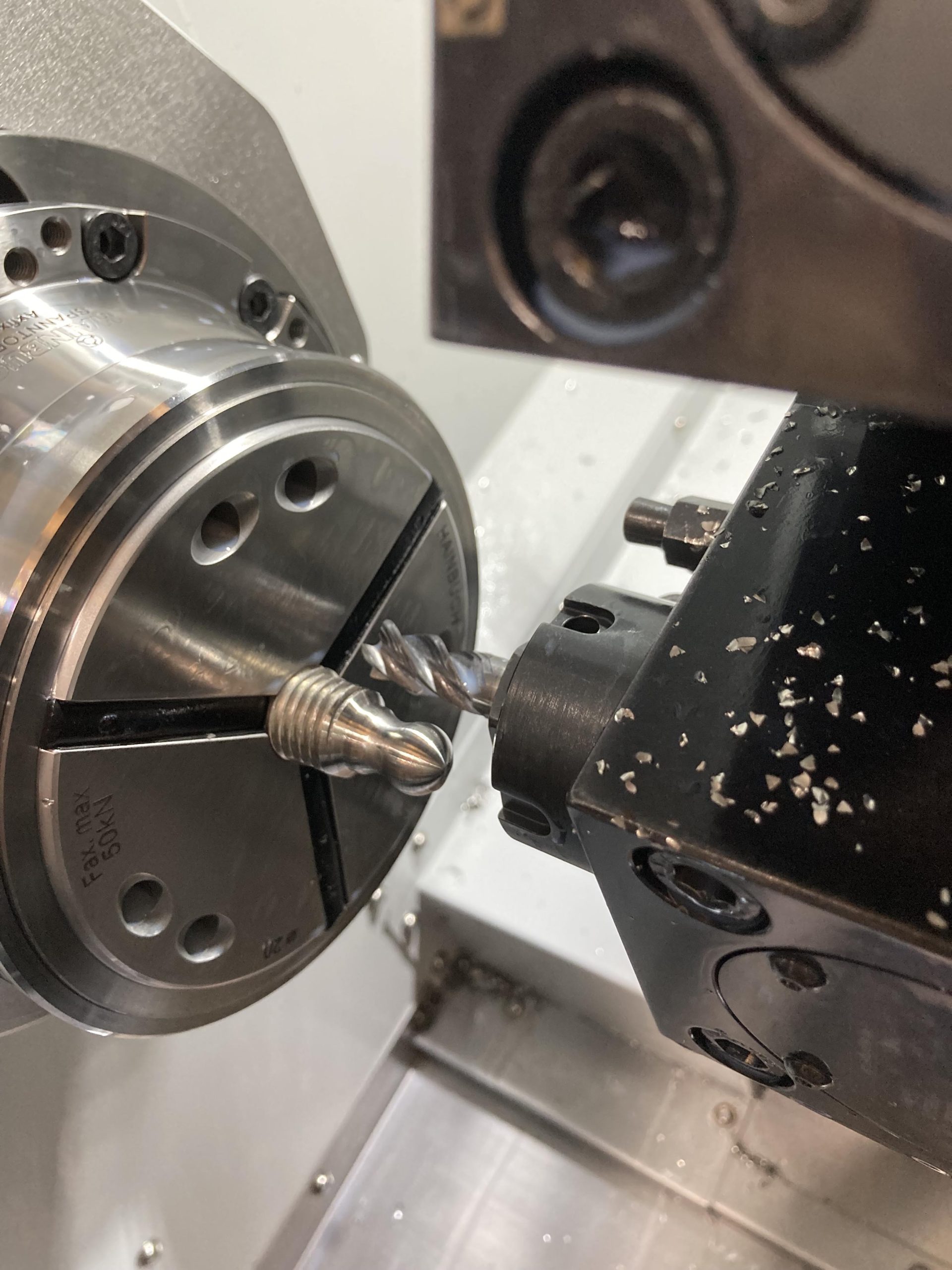
The Lynx 2600SY – a closer look
The Lynx 2600SY is a flexible, popular and proven multi-tasking turning centre with a 380mm maximum turning diameter and 610mm maximum turning length.
The machine features fast 30m/min rapids (X- and Z-axis) and is equipped with a powerful, high-torque spindle (18.5kW/3500rpm/403N-m), as well as a 12-station (24-position), servo-driven turret with 5,000rpm driven tooling capabilities.
The Lynx 2600SY’s versatility is delivered, in part, via its integrated 6” chuck sub-spindle (4500rpm) and its +/-52.5mm Y-axis.
The machine, supplied to Arnott Handling, has the advanced Fanuc i Plus CNC control with a 15” touchscreen and iHMI user interface and, in addition to the bar feeder, was also equipped with a FilterMist extraction unit, a quick-change Hainbuch 80 Mini Axfix dead-length collet chuck, an auto tool-setter and a bespoke parts catcher, designed to handle larger components.
Arnott Handling: the Future
Arnott Handling is experiencing strong growth and, to ensure it is able to meet future demand for its products, is executing a growth plan that will see it streamline its existing processes and invest in new machine tool and automation technologies to maintain its competitive edge.
In conjunction with its successful in-house Apprenticeship Programme, these investments will also help limit the potential impact and effects from a shortage of skilled labour that many UK manufacturers are currently experiencing.
The company’s recent investment in the DN Solutions’ Lynx 2600SY with an integrated bar feeder is a case in point and demonstrates the company’s future direction of travel.