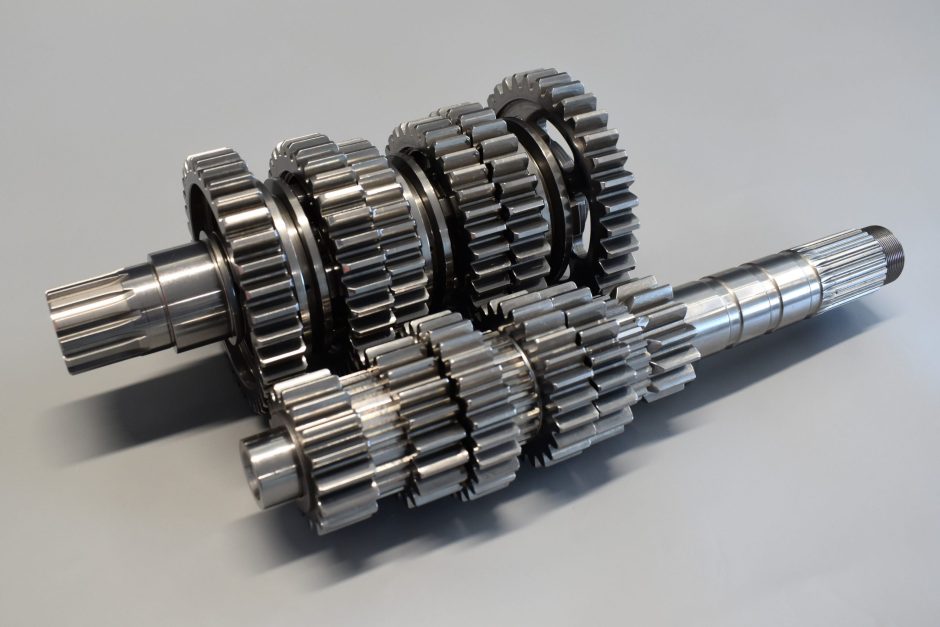
Leading motorcycle transmission and gearbox design and manufacturing specialist, Nova Racing Transmissions, invests in a new high-performance lathe from Mills CNC.
The new lathe’s arrival has significantly strengthened the company’s in-house turning capacity and capabilities, helping reduce production bottlenecks and improve process efficiencies.
Mills CNC, the exclusive distributor of DN Solutions’ and Zayer machine tools in the UK and Ireland, has recently supplied leading motorcycle transmission and gearbox design and manufacturing specialist, Nova Racing Transmissions Ltd., with a new, high-performance DN Solutions’ lathe from Mills CNC.
The machine, a compact, Fanuc-controlled 8” chuck Lynx 2100LMB, was installed at the company’s manufacturing facility in Partridge Green, West Sussex in December 2024 and has replaced an older Daewoo lathe that, although still working satisfactorily, was slow and cumbersome to use.
Since being installed the new Lynx 2100LMB, equipped with driven tooling capabilities, has been put through its paces machining a range of high-precision motorcycle ‘close ratio’ gearbox components (input and output shafts, gear blanks, dog rings, collars etc.), in small batches for a diverse range of domestic and international end user customers.
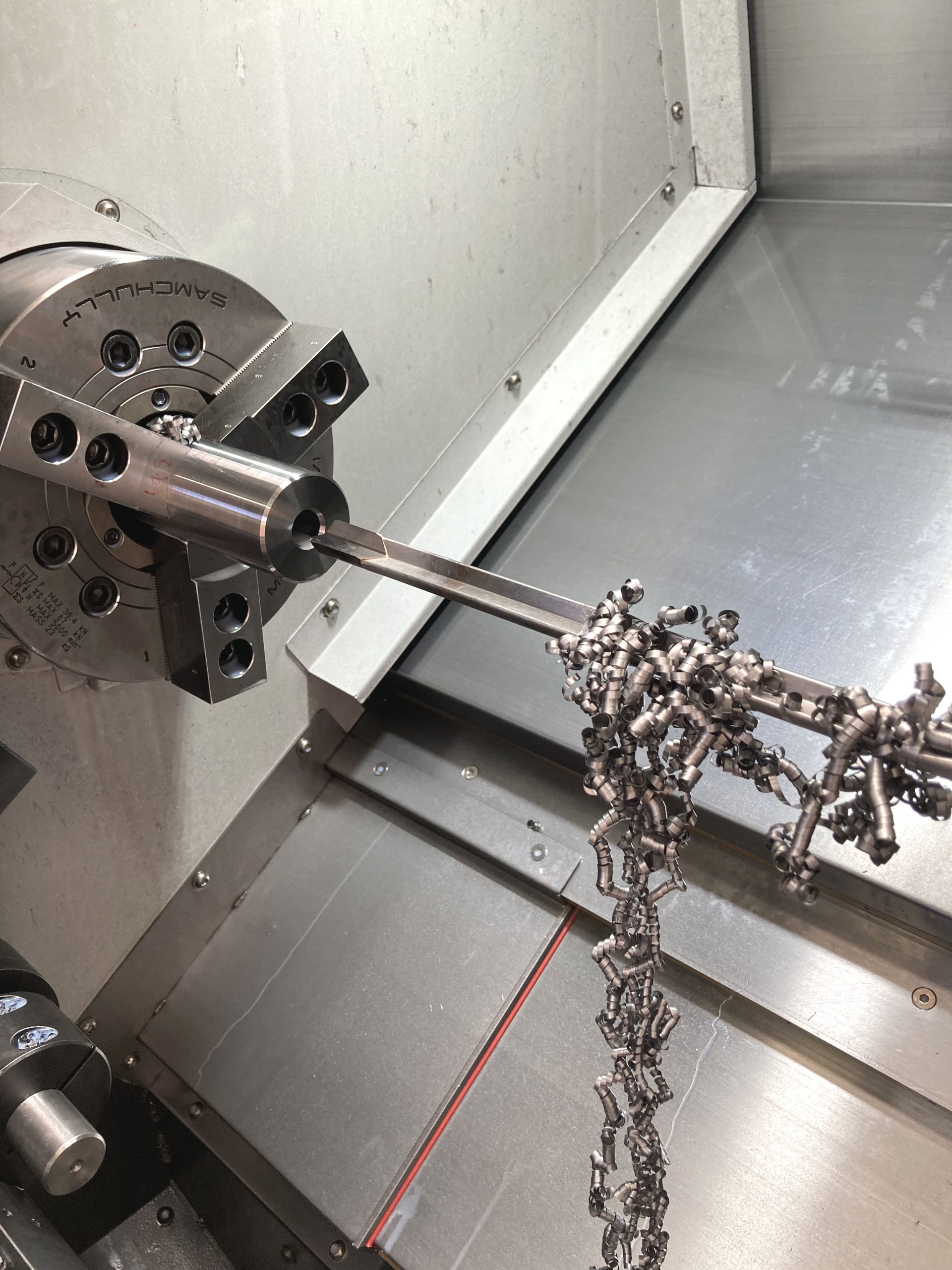
Customers include teams and riders competing in the British Superbike (BSB), World Superbike (WSBK), Isle of Man TT and Motocross championships etc., as well as for motorcycle OEMs, motorbike racing clubs and individual motorcycle owners, enthusiasts and engine builders.
Components are also made for stock enabling the company to quickly supply customers with spare and replacement parts.
Batch sizes machined on the Lynx 2100LMB vary from one-and two-offs through to 10-off, and can also include prototypes and pre-production parts.
Specific parts machined on the Lynx 2100LMB include input and output shafts – essential components for every motorcycle’s transmission systems (i.e., superbikes, classic bikes, road bikes, off-road bikes etc.).
These shafts are made from a tough and durable case hardening motorsport steel alloy which is supplied to Nova Racing in pre-cut rough bar stock from high-performance steel specialist, Bohler Steels.
Following the machine set up, soft turning operations undertaken on the Lynx 2100LMB start by first reducing the diameter and length of each pre-cut bar. With 50mm diameter bars, for example, typically 1mm is taken off the OD and 3mm off the length (e.g., 1.5mm from each end).
Other operations, prior to heat treatment, include gun drilling on each shaft’s centre line using high-pressure coolant to create a long narrow through bore hole with a high depth-to-diameter ratio.
There can be up to six soft turning operations (drilling, thread turning etc.), performed on each shaft before heat treatment. Cycle times are short (up to 2 -3 minutes), and accuracies vary, according to each turned feature, and are typically +/- 0.1mm. (Tighter tolerances i.e., down to 10 microns are required in hard turning operations).
“Prior to acquiring the new Lynx 2100LMB, gun drilling operations on gear shafts were all performed on one of our older Lynx lathes, a long-bed Lynx 220LMA, acquired in 2014.
“When we were busy, which was (and still is) the norm rather than the exception, the over reliance on just one machine to perform such a critical machining process was not ideal and created production bottlenecks that were adversely affecting efficiencies and our ability to meet customers’ lead times.
“As intended, the investment in the new long-bed Lynx 2100LMB has provided us with additional turning capacity, enabling us to eliminate this specific production pinch point, enabling us to become more productive and efficient as a consequence.”
Daniel Vaughan, Engineer at Nova Racing Transmissions
Complex production scheduling
The interconnectedness and interdependency of Nova Racing’s complementary machining and manufacturing processes means that there really cannot be a ‘weak link’ in the company’s production chain.
Take the gear shafts mentioned above. Once gun drilling operations have been completed, the shafts are then moved to Nova Racing’s hobbing machines where a series of high-precision splines are machined on each shaft’s external OD surface.
Once completed, and de-burring operations have been performed, the machined shafts are then sent out in batches for heat treatment, by an external supplier, before being returned to Nova Racing for ‘hard’ finish turning operations performed on the Lynx 2100LMB.
“Production scheduling can be a challenge at the best of times. There are lots of moving parts, and there needs to be some flexibility built into our processes to cope with unexpected, last minute and priority jobs.
“If components are waiting in limbo for a lathe, machining centre, hobbing machine or gear cutting machine etc., to become available, or for heat treatment processes to be completed, the efficiency of our whole operation is affected.”
Daniel Vaughan, Engineer at Nova Racing Transmissions
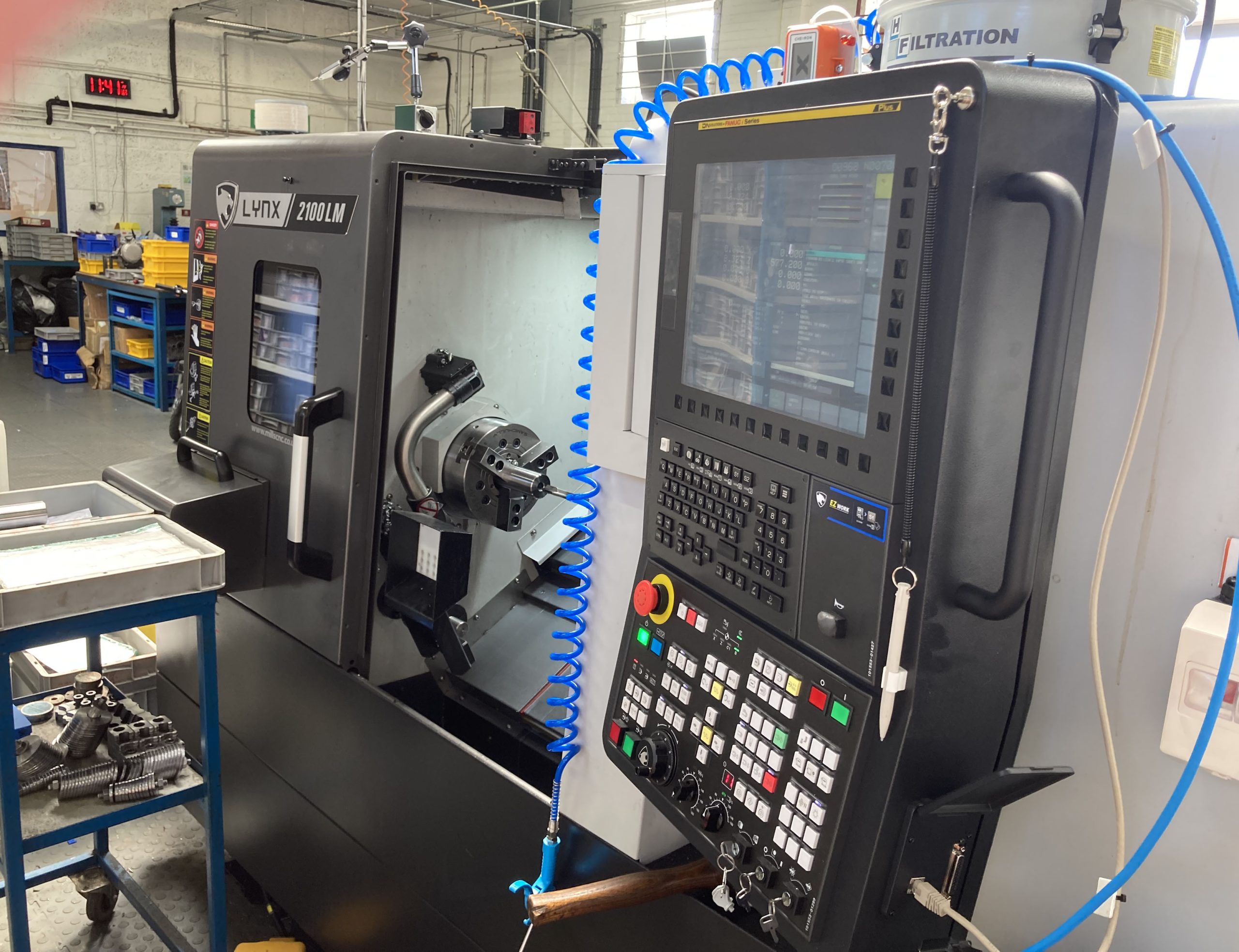
Nova Racing and Mills CNC
Since 2012, which coincided with the company relocating to its current facility, Nova Racing has relied on DN Solutions’ (previously Doosan) Lynx lathes from Mills CNC for its small turned part processing requirements.
So, when Nova Racing, a company committed to continuous improvement, identified the need to invest in a new compact lathe back in 2024, it was not surprising that Mills CNC was one the first machine tool suppliers approached.
“We have developed good relationships with Mills CNC over the years. Our previously acquired Lynx lathes are fast, powerful, precise and flexible. They are reliable and competitively priced, and the pre- and after-sales service and support we receive from Mills CNC cannot be faulted.”
Daniel Vaughan, Engineer at Nova Racing Transmissions
Although Nova Racing approached three machine tool suppliers to provide quotes for the new lathe, the decision was made to go with Mills resulting in an order being placed for a Lynx 2100LMB – a long-bed lathe with live tooling.
Lynx 2100LMB – a closer look
The Lynx 2100LMB is a popular and proven compact lathe, ideal for fast and accurate small parts processing.
The machine has a rigid design and build and, despite its small footprint, provides customers with a 300mm maximum turning diameter and a 290mm maximum turning length.
In addition to being equipped with a 15kW/15,000rpm spindle, a 12-station, servo-driven BMT45 turret, roller-type LM guideways, a tailstock and 3.7kW/6000rpm driven tooling capabilities, the Lynx 2100LMB also features the advanced Fanuc iPlus control with 15” touchscreen iHMI.
The Lynx 2100LMB supplied to Nova Racing also featured a MH500 swarf conveyor system, 20bar through-spindle-coolant capability and an auto tool setter.